In 2014, the year VILS was founded, we took on on a challenge that was as complex as it was groundbreaking: Designing and building the world’s first GMP-certified mRNA production facility.
And we delivered: The facility was completed on a tight, 16-month timeline, years before mRNA technology became a global game-changer with COVID-19 vaccines.
Our client in this venture was Etherna, a Belgian biotech company founded in 2013 and focused on mRNA-based immunotherapies. As a new enterprise at the time, bringing us in was one of its first major strategic decisions. The facility spans 300 square meters and was designed to cGMP specifications. It was purpose-built to manufacture mRNA-based immunotherapies for Phase 1 and 2 clinical development programs as well as preclinical studies.
Relying on deep process knowledge.
At the time, no regulations existed for commercial mRNA facilities, and clinical trial guidelines didn’t cover full-scale manufacturing. To achieve GMP certification, we had to move beyond standard methods. A risk-based design founded on deep process knowledge was the only viable way to design a compliant facility.
The first step was to understand Etherna's process by asking the right questions: What does the process need? How would the mRNA be handled? What should the workflows look like? What are the risks? How do we eliminate those risks while keeping the design lean and practical? These were some of the questions that guided us.A facility built on the essentials
From there, we built a facility that focused on the essentials: The science and the specific requirements of Etherna's processes. We were able to create a facility compliant with GMP standards because we could justify every design decision to regulators.
The design also had to be lean and practical for the operators. So, we used pass-through boxes to streamline cleanroom flows, for example. The facility still included multiple cleanroom grades, but this approach eliminated the need for operators to repeatedly gown and re-gown between areas. That saved processing time, which was an advantage for mRNA stability in the cold chain, and minimized operational inefficiencies.
Business focus to enable innovation
Larger, more complex facilities can be prohibitively expensive, so we focused on delivering a lean, affordable solution.
This process-focused and business-focused approach has been standard operating procedure at VILS ever since. We don’t just build facilities to meet theoretical requirements. We design them to meet the specific, identified needs of each client, ensuring that their facility isn’t just compliant but practical – and operator-friendly.
An inflection point for mRNA production
The Etherna project was more than just a first – it marked a milestone for mRNA production. When global demand for mRNA vaccines surged, Etherna's facility was already operational. It’s a testament to what process-driven design can achieve, even in uncharted territory.
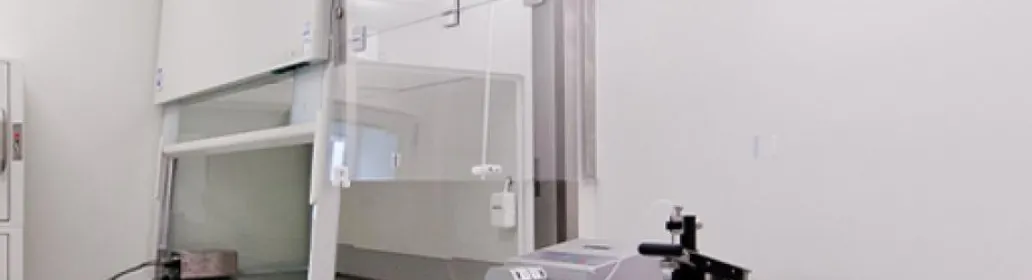
ATMP and Linked Industries
Cutting-edge therapies bring new hope
Cutting-edge therapies bring new hope