For Novasep, a leading CDMO and supplier of services and technologies for the life science industry, the fill & finish commercial facility we designed and built was the final piece of its new, €27 million viral vector production facility in Seneffe, Belgium.
Novasep’s flagship facility, known as Senrise-IV, was an operational and strategic step forward for Novasep. It was one of the early facilities to feature the integrated bioproduction of viral vectors at commercial industrial scale. It includes two cGMP production lines: One is dedicated to adherence cell culture for viral vectors in moderate quantities – to treat certain rare diseases or for lower dose indications – and one for suspension cell culture with bioreactors of 50 to 2,000 liters to produce larger quantities.
Senefill’s operations, which came onstream on 1 October 2019, support key biopharmaceutical markets for Novasep and its clients with cell and gene therapies, oncology, vaccination and other innovative therapies. The 1,800m² unit has a 400m² area dedicated to filling a wide range of biological products, including viral vectors, monoclonal antibodies and other biologics.
It features semi-automatic and automatic liquid filling machines under isolators and can deliver up to 10,000 vials per session, with operational capability of two-to-three sessions per week.
Co-locating both facilities on a single site optimizes manufacturing workflow integration for viral vector production. This integrated approach enables either standalone fill & finish services or combined drug substance and drug product manufacturing.
“Zero-risk” approach
When building Senrise-IV, Novasep implemented a zero-risk approach with distinct separation of production zones and onsite decontamination systems for effluent and materials. The 2,000m² Senrise-IV facility meets the highest cGMP standards governing commercial biopharmaceutical production.
Our engineering team was tasked with meeting these same, stringent requirements, while adhering to the established, 16-month timeline from start to a commissioned, GMP-certified facility – a significant challenge that we successfully met.
To meet Novasep’s zero-risk standards on the tight timeline, we employed a focused approach, prioritizing essential elements. Following design approval, we carefully selected contractors who could deliver a facility that could be built and approved on time. Our design was lean in terms of the fit-out of the installations and the flows around it, as well as optimized to Novasep’s precise needs.
Applying our viral vector expertise
A critical success factor was to fully understand Novasep’s process for viral vectors. When we constructed Senefill, viral vector technology was relatively novel, with limited industry experience.
However, our team had already designed a GMP-certified viral vector facility, providing us with essential expertise. This enabled us to translate Novasep’s process requirements into a facility with lean, efficient process steps that optimized production flows.
Built-in flexibility for future products
It's also important for a CDMO that facilities be designed with enough flexibility to handle future products and to consider how people will fit into the picture. The goal is a process that is operator-friendly and does not complicate how people have to work. That is something we also translated into the layout and facility design.
The Senefill facility that we delivered represents a significant advance in manufacturing capability for targeted and innovative therapeutics, and we consider it a major success, especially in light of the high standards and ambitious timeline. The facility commenced operations on October 1, 2019, enabling Novasep to meet growing demand for advanced therapeutics.

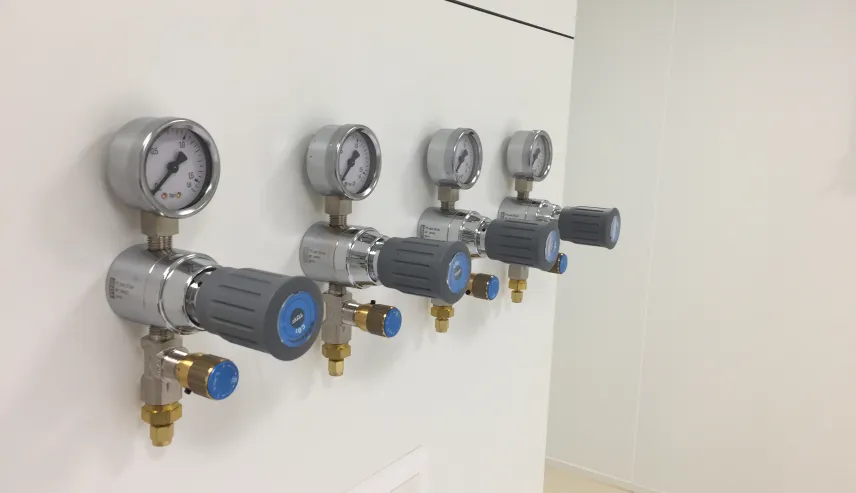
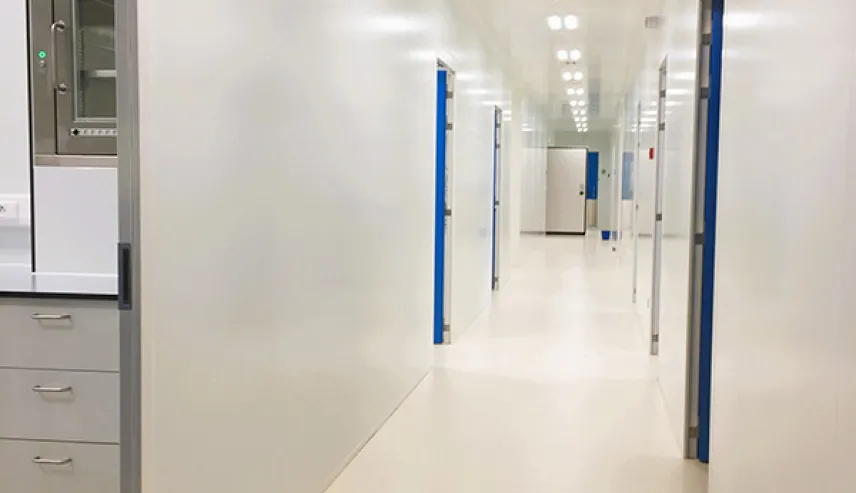
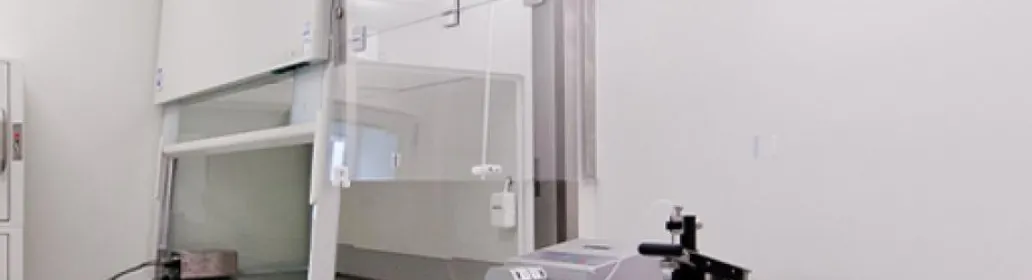
BIOLOGICALS & VACCINES
High complexity, high impact
High complexity, high impact